Injection molding is a popular manufacturing process for producing luggage due to its efficiency and versatility. However, it also has its own set of advantages and disadvantages. Here are some of them:
Advantages of Injection Molding for Luggage:
- Cost-effective: Injection molding allows for high-volume production at a relatively low cost per unit. Once the molds are created, the cost of each individual luggage item decreases significantly, making it an economically viable option for mass production.
- Design flexibility: Injection molding enables the creation of complex and intricate designs, including patterns, textures, and brand logos, in luggage. The process allows for the incorporation of various features such as compartments, handles, wheels, and telescopic handles, giving manufacturers the freedom to create functional and aesthetically appealing luggage.
- Material selection: Injection molding supports a wide range of materials, including various types of plastics and composite materials. Manufacturers can choose materials that offer the desired properties, such as durability, impact resistance, lightweight construction, water resistance, and UV resistance.
- Consistent quality: The injection molding process ensures consistent and uniform production of luggage items. The use of molds guarantees that each piece will have the same dimensions, weight, and structural integrity, resulting in a reliable and high-quality end product.
- Efficient production: Injection molding is a highly automated process, allowing for efficient production with minimal human intervention. The cycle time for each mold is relatively short, enabling high production rates and faster turnaround times.
Disadvantages of Injection Molding for Luggage:
- High upfront costs: The initial investment required for creating molds can be substantial. Designing and manufacturing molds specific to luggage designs can be costly, especially for small-scale or custom productions. This cost can limit the feasibility of injection molding for some manufacturers.
- Design limitations: Although injection molding offers design flexibility, there are still some limitations to consider. Complex designs or intricate details may require additional mold features or post-processing steps, increasing the cost and complexity of production.
- Long lead time: The process of creating molds for injection molding can take time, especially for complex designs or when modifications are necessary. This can result in longer lead times between the initial design phase and the actual production of the luggage.
- Material limitations: While injection molding supports a wide range of materials, certain specialized materials may not be suitable for this process. For example, if a luggage design requires materials with unique properties or textures that cannot be achieved through injection molding, alternative manufacturing methods may be necessary.
- Environmental impact: Injection molding typically utilizes plastics, which can have a negative environmental impact due to their non-biodegradable nature. However, efforts are being made to develop more sustainable materials and improve recycling processes to mitigate these environmental concerns.
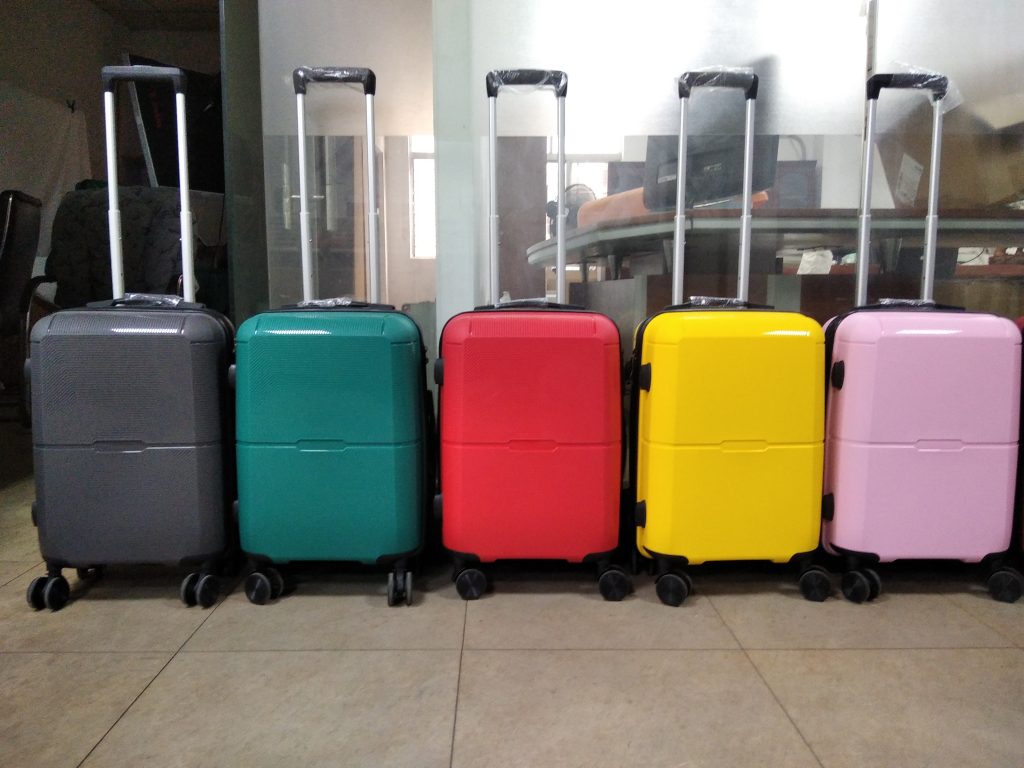
It’s important to consider these advantages and disadvantages when deciding whether injection molding is the right manufacturing process for luggage, as specific requirements and production scales can influence the feasibility and suitability of the process.